Intonachino Fine, Medio or Grosso
Intonachino is a natural traditional decorative finish with a sense of simplicity that has made it the most popular outdoor finish in Italy. In the manufacturing of our Venezia Stucco materials, we attach great value to the quality of the materials, ease of application and a customized colouring system. The range of additives makes it possible to modify the characteristics of the products and vary the aesthetic effects of our marmorino.
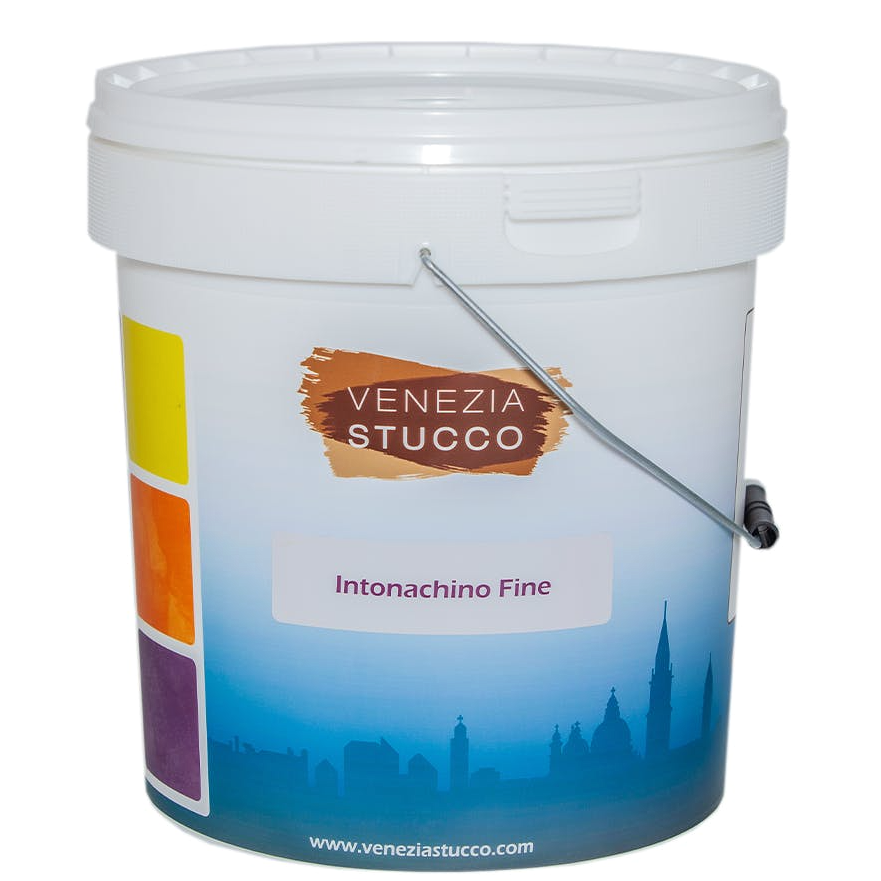
Informations and use of Intonachino
Intonachino is a rough plaster, more or less fine, that is appreciated for its soft light and dark shades, known as chiaroscuro.
It is available in fine, medium and grosso (coarse) textures and can generate different effects.
The finer version is often used in interiors where a warm looking plaster is required.
Breathable, naturally anti-mould, for indoors and outdoors.
Colour
Ready to use in white, can be coloured with our colour system or customized for any requested colour.
Packaging
- Intonachino Fine, Medio or Grosso kg 24 bucket.
Composition
Lime and selected marble powder. Various additives (less than 2%)
Application cycle
- Preparation of the walls with our Quartz Primer (drywall, wood or any smooth surface) or Normal Primer (rough surface or lime base plaster). They can be applied by roller or brush.
- On a completely dry base coat of Intonachino the next day apply by trowel two coats using more or less 2,4 kg per m².
Protection
Protect with our Waterproofer
RELATED PRODUCTS
Protective and Auxiliary Products
(links to the products)
Quartz Primer -
Primer Normal
Thickener
Decorative Additives
(links to the products)
Terracotta for Veneziano Medio
Instructions for the lime-based Venezia Stucco products
Our lime-based products should be applied to a plaster (rough or smooth, new or not insulated).
Already painted surfaces require a thorough brushing down to remove dust and uneven parts.
Where necessary, use a brush or roller to apply a coat of Quartz Primer, or Normal Primer diluted 1 to 7/8 with water.
Apply at least three coats of the lime-based product.
NOTE:
- water on the surface of the material into the bucket is normal, and should be removed before use or addition of colorants.
- all
lime-based products lose their viscosity when shaken, and need a period of 6/12 hours after mixing to regain their density. The product is very dense, and ready for use, thus it may be necessary to use an appropriate drill attachment to stir for a few minutes to reduce viscosity. Choose the
colour. Add all of the COLOUR ADDITIVE to the container and continue mixing until a homogeneous shade is obtained. Let the product rest for about 6/12 hours before using.
Suggestions for the application of lime-based plasters like our Intonachino:
These are suggestions to always keep in mind when applying Marmorino, Intonachino and other lime-based products.
A lime plaster (and also cement) changes color depending on its drying time. However, the general rule of thumb is that the slower it dries, the darker the resulting color. With marmorino, a darker tone is also related to how much pressure is applied during the polishing phase.
It is customary to recommend applying lime plasters at a minimum ambient temperature of 5°C (41°F), but experience has shown that if you want to avoid color differences, the minimum temperature should be higher.
This is also linked to two other factors: the relative humidity of the air which determines drying time and, consequently, the tone of the color, and finally, and just as important, the absorption of the substrate.
Therefore, when applying lime plaster, you have to take into account these three factors.It is difficult to give precise guidelines. It depends a lot on the experience of the technician, who in any case has to keep in mind these factors and understand the characteristics of the materials.
For the substrate: the ideal plaster is one which has the same amount of absorption over its entire surface. If there are areas of concrete under the plaster (for example, around windows or along the area where two floors of a building meet), it’s possible that with a thin layer of plaster, there will be different amounts of absorption. If the temperature and humidity are good enough to ensure a rapid absorption, these differences in absorption rates won’t affect the color. But if there are low temperatures or high humidity, the areas which absorb more slowly will become darker.
It is always recommended to apply primer first. This is not really enough to guarantee an equal absorption rate over the entire area, but is always a good idea. The quality of the primer is especially important when conditions are at a minimum.
Remember that only an experienced technician can guarantee good results. However, if there is one rule, independent of the absorption of the substrate, the humidity should be about 84% and the temperature should not go below 7°C (45°F). Obviously, if the humidity goes up, the temperature should go down.
Always keep in mind that the temperature and humidity should stay within these recommended limits for the entire drying time. The technician could forget that if he finishes applying the material in the afternoon, it could undergo colder temperatures during the night which would push it beyond the recommended limits before drying is complete.
One last thing to remember is that the wind can also play a role and can help to accelerate drying time.
Naturally if the substrate has a uniform absorption and you do all the work on one side of the building on the same day, you can go to the edge of the recommended limits since a small change in color from one side to another won’t be visible.
A brief history of lime as building material
Lime has been used for nearly two thousand years in the construction of foundations, floors and especially in particularly humid environments such as coatings of aqueducts and water pipes. Alongside these structural works it has been used for wall coverings such as mortars, interior and exterior plasters and in various types of decorative applications.
First, a brief mention of lime mortar chemistry, the production of which is basically a three-step process:
- Calcination: When limestone/chalk (calcium carbonate) is burnt in the kiln it turns into quicklime (calcium oxide) and releases carbon dioxide.
- Hydration: Water is added to quicklime/burnt lime to produce hydrated lime (calcium hydroxide). Carbonation: Over the lifetime of lime products, carbon dioxide is gradually re-absorbed by lime from the air, which is also known as “re-carbonation”, as, chemically, this begins to turn the lime back into calcium carbonate, essentially the opposite of the calcining/burning process.
The beginning of the use of
lime in mortars is unclear, however in 4000 BC. the Egyptians discovered that limestone, when burned and combined with water, produced a material that hardened with age. The first documented use of this was when the pyramids were plastered with a lime-based plaster.
An extensive use of
lime mortar occurred when it was adopted by the Greeks and later by the Romans around the first millennium BC. It is not clear when the Romans started using lime mortar, but around 150 BC. it was common practice. The Romans developed a hydraulic-setting lime mortar with the addition of crushed
ceramics,
crushed brick (coccio pesto) or volcanic ash (pozzolana -pozzolanic ash) within the mortar mix.
The earliest most important references to lime mortar come from Vitruvius' De Architectura, written around 25 BC.
Vitruvius, specifies a ratio of 1 part lime and 3 parts pozzolan for the lime mortar used in buildings and a 1: 2 ratio of lime and pozzolan for underwater works.
Lime mortar continued to be used from the Roman Empire until about the 19th century, where it was superseded in use by Portland cement mortars.
But, although technology has developed new construction products,
lime mortar is still widely used as a greener construction option than concrete. For both modern and historic homes, it offers a number of advantages that make it highly competitive over alternatives.
Among the most important advantages we have:
-Workability:
Lime mortar has great plasticity. This makes it easy to work with and suitable for modelling in decorative environments.
-Does not separate:
Lime is an excellent
binder. This prevents the mortar from crumbling over time, ensuring its resistance to bad weather.
-Lime is also used to repair traditional buildings that were originally built with lime mortars, this is because lime allows for greater movement without cracking or damaging the original masonry -Lime can also be a great solution to moisture problems as it absorbs water and releases it reducing the chances of water getting trapped and damaging the building.
Origin and Evolution of Marmorino
Over time,
Marmorino, the traditional
lime-based
polished plaster finish, has been given a variety of different names: Polished Plaster, Italian Stucco Plaster,
Venetian Stucco, Stucco Lustro, - and many others.
Marmorino is made with
lime mixed with
marble powder and used as a finishing
plaster.
It is worked in a way to imitate the texture and brilliance of marble surfaces.
Marmorino is well known as a classic
Venetian
plaster but its origins are lost in the mists of time. Of all the ancient peoples, the one who made the most extensive use of stucco was the Roman people.
Vitruvius describes this technique accurately in his multi-volume work entitled “De Architectura” (1st century BC ).
It should be noted that the
Marmorino was properly white deriving from a mixture of
lime and
white marble or
stone powder. Among the Romans the colouring took place mostly with the fresco technique, not in the mixture as will be done to a large extent starting from the eighteenth century. In the archaeological excavations of Pompeii and Herculaneum and in various ancient Roman structures in addition to the cycles of frescoes painted on
Marmorino
plaster, famous for the chromatic quality and the mastery of the execution, we also find the extensive use of
Marmorino to ennoble otherwise poor surfaces, such as brick columns, walls of thermal baths, houses, and mausoleums.
This type of
plaster also had the advantage, thanks to the use of stones and marble residues from the work on site, of replacing the use of quarry stones and
marbles with the relative costs of extraction, transport and reduction in blocks.
Marmorino was rediscovered centuries later after the discovery of Vitruvius ancient treatise in the 15th century.
This 'new'
plaster responded well to the aesthetic needs of the classical ideal which in the fifteenth century had become fashionable especially in the
Venetian lagoon area.
This elegant
finish that simulated the noble material of the stone will characterize much of Venetian Renaissance architecture. It covered both the
interior and
exterior of the brick structures, embellishing the masonry surfaces by delimiting and camouflaging itself with the parts made of Istrian stone, (the same stone widespread as a building material throughout the
Venetian area, that was added ground in the Marmorino in the ways described by Vitruvius.)
The
Marmorino also characterized the architectural works of great artists of the sixteenth century who worked in the Veneto region such as Sansovino, Palladio and many others. In
Venice the churches of San Giorgio and Redentore, but also the
Venetian villas like Villa Foscari called “La Malcontenta”, Villa Barbaro on the hills of Maser and Villa Almerico Capra, also known as “la Rotonda”, are all works appreciated throughout the world also for their precious
finish.
In the eighteenth century, the use of painting the surface of the Marmorino with the fresco technique was replaced by mixing the pigments, resistant to the causticity of lime, directly in the mixtures used for the various layers that make up the
Marmorino. This is the origin of the typical pastel colors still present in several villas, palaces and churches where the original
Marmorinos of the time are kept.
The
Marmorino will also find use in the linear sobriety of neoclassicism, where the rediscovery of the purest classical elements echoes.
Marmorino maintained its prestige for centuries until the end of the 1800s when interest in it waned and it was considered only an economic solution to the use of
marble. Only at the end of the 1970s, also thanks to the use of
Marmorino by the architect Carlo Scarpa from
Italy, this finishing technique returned to the interest of the best modern architects. In recent times, the search for ecological materials with low environmental impact has led to a further re-evaluation of this wonderful plastic material for
finishing and architectural embellishment.